ABOUT US
Leading the Way in Textile Manufacturing
Welcome to The Kamal Mills Private Limited, where innovation meets tradition in the world of
textiles. Established with a passion for quality and craftsmanship,
we are a leading provider of premium fabrics that cater to a wide range of industries, from fashion
and home décor to upholstery and beyond.
We believe that textiles are not just materials—they are an expression of creativity, functionality,
and sustainability. Our team works closely with designers, manufacturers, and suppliers to create
fabrics that not only meet but exceed the expectations of our clients. Whether you’re looking for
custom solutions or ready-made collections, we offer a diverse range of textiles tailored to suit
every need.
Years
Experience
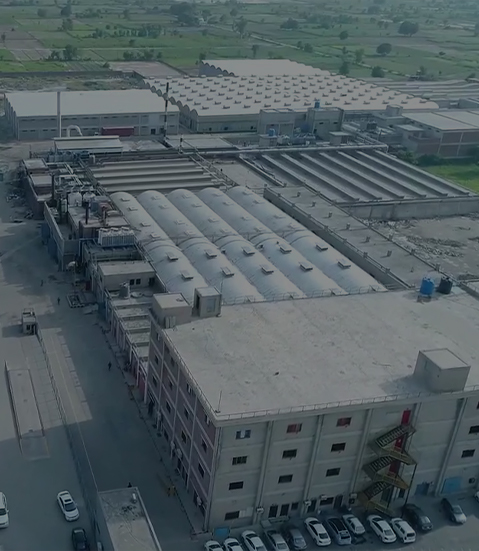
WHAT WE DO
Crafting Quality Products for Every Need
Socks Manufacturing
With decades of expertise, we produce socks that provide both comfort and performance for all occasions.
Towels Manufacturing
Our manufacturing process ensures every piece of towel meets the highest standards of quality and comfort.
Yarn Dyeing &
Covering
Our yarn dyeing process combines traditional craftsmanship with modern technology for unmatched strength and softness.
Faisalabad, Pakistan
3 Km Jhumra Road Khurrianwala, Faislabad, Punjab, Pakistan.
Email: marketing@kamal.com.pk
Call directly:
+92 41 436 2814-5